Hydrogen Production -
PEM Electrolysis
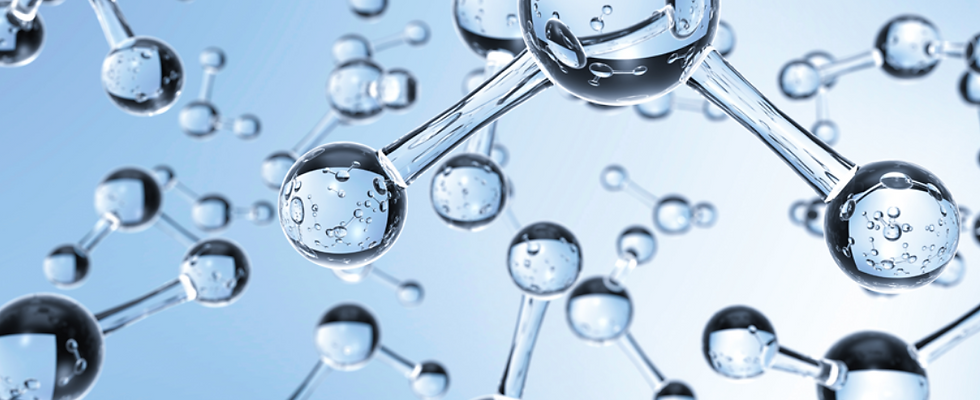
Overview
The most established technology options for producing hydrogen from renewable energy sources are water electrolysis and steam reforming of biomethane/biogas with or without carbon capture and utilisation/ storage (CCU/CCS), is less mature pathways are:
-
Biomass gasification and pyrolysis.
-
Thermochemical water splitting.
-
Photocatalysis.
-
Supercritical water gasification of biomass.
-
Combined dark fermentation and anaerobic digestion.
Hydrogen production by Electrolysis
Three main electrolyser technologies are used or being developed today. This section provides a brief overview of the technology outlook for electrolysers or detailed modelling of their performance and related impact on the cost of hydrogen production. The industry has used alkaline (ALK) electrolysers for nearly a century. Proton exchange membrane (PEM) electrolysers are commercially available today and are rapidly gaining market traction as, among other factors, they are more flexible and tend to have a smaller footprint. Solid oxide electrolysers hold the potential for improved energy efficiency but are still in the development phase and, unlike ALK and PEM, work at high temperatures.
ALK and PEM electrolysers compared
ALK electrolyser technology is fully mature. It has been used by industry since the 1920s for non-energy purposes, particularly in the chemicals industry (e. g., chlorine manufacture). By contrast, PEM electrolyser technology is rapidly emerging and entering commercial deployment. Past development and established production volumes have resulted in average capital expenditure (CAPEX) being lower for ALK electrolysers than for PEM electrolysers on a per kilowatt basis. The CAPEX for PEM, however, has been dropping significantly in recent years.
The lifetime of an ALK electrolyser is currently twice as long and is expected to remain significantly longer for the next decade. Table 1 below provides a general overview of the techno-economic characteristics of ALK and PEM electrolysers today and their desired future improvements.5 State-of-the-art PEM electrolysers can operate more flexibly and reactively than current ALK technology. It offers a significant advantage in allowing flexible operations to capture revenues from multiple electricity markets. PEM technology provides a more comprehensive operating range and a shorter response time. Systems can be maintained in stand-by mode with minimal power consumption. They can operate for a short period (10– 30 minutes) at a higher capacity than the nominal load (beyond 100 %, up to 200 %). With both upward and downward regulation capability, a PEM electrolyser can provide high-value frequency containment reserve (FCR) capacity without sacrificing available production capacity. In other words, operators of PEM electrolysers can supply hydrogen to their clients (for industry, mobility or injection into the gas grid) while still being able to provide ancillary services to the grid with low additional CAPEX and OPEX, provided that sufficient hydrogen storage is available (NREL, 2016a; NREL, 2016b).
This enhanced flexibility could improve the overall economics of power-to-hydrogen, providing a new revenue stream from multiple electricity markets to compensate for the higher capital cost of PEM compared to ALK electrolysers. However, the ancillary services market is currently experiencing strong competition, reflected in significant price reductions, which might affect the business case for electrolysers in the medium term. PEM electrolysers produce hydrogen at a higher pressure (typically around 30 bar) than ALK electrolysers, which produce hydrogen at atmospheric pressure (up to 15 bar). As a result, the need for downstream compression to reach the desired end-use pressure is lower; this is particularly relevant in applications where high-pressure matters, such as mobility.
SOEC electrolysers compared to ALK and PEM
SOEC technology holds the promise of greater efficiencies compared to ALK and PEM. However, SOEC is a less mature technology, only demonstrated in the laboratory and small demonstration scale. Its investment costs (CAPEX) are currently higher; however, SOEC production mainly requires ceramics and a few rare materials for their catalyst layers, while PEM electrolysers need significant amounts of platinum for their catalyst layers. The need for high-temperature sources of heat close by might also limit the long-term economic viability of SOEC – for which the only renewable sources are likely to be concentrated solar power (CSP) and high-temperature geothermal. SOEC can potentially be a game-changing technology in the medium term. Its advantages are expected to include increased conversion efficiency and the possibility of producing a synthesis gas directly from steam and COâ‚‚ for use in various applications such as synthetic liquid fuels.
Harnessing synergies with CSP plants, which co-produce steam and electricity on site from solar irradiation and have a high capacity factor, is one pathway to ensuring all energy inputs are entirely renewable. PEM electrolysers' full flexibility benefits and systemic added value can only be captured if they are grid-connected. This configuration is also the most competitive because it enables the operator to capture ancillary service revenues and optimise the utilisation rate and electricity purchases for different LCOH at current technology cost levels and in 2025 for a PEM electrolyser of 20 megawatts (MW)10 connected to different electricity sources:
​
-
The grid in Denmark (in 2017)
-
An offshore wind farm in the North Sea
-
A large-scale solar PV plant in the United Arab Emirates
-
A combined solar and wind farm in Chile
​
With respect to grid connection, the PEM electrolyser is assumed to be able to participate directly in the electricity market, which is only likely to be the case if the electrolyser is installed within an existing industrial plant and its power portfolio; as a stand-alone plant, the unit is expected to be too small to operate directly in the market. ALK technology is not as flexible as PEM and might not follow fluctuating generations from VRE. The only scenario considered is ALK electrolysers run as grid-connected (without accounting for any revenues from grid services) [1].
Comparative Analysis of Technologies
Rational
​
Scalability, hydrogen production rate and environmental impact have been given the highest weightage. Scalability being the highest weightage as the key towards large-scale commercial success, the technology should remain feasible and reduce the operational cost when scaled up. Production rate and environmental impact are also significant factors when considering large-scale production. Although Alkaline electrolysis is easily scalable and directly adopted, there are other options for hydrogen production due to the high load of caustic waste and the need to have auxiliary units to enhance the hydrogen purity.
SOC was not chosen due to its lower technology readiness level; this implies that the cost of setting up a hydrogen production facility will be much higher and may need to be more scalable with the current advances. PEM stands out as an optimal choice by balancing out all the critical factors
Reference
[1] Guo, Y., Li, G., Zhou, J. and Liu, Y. (2019). Comparison between hydrogen production by alkaline water electrolysis and hydrogen production by PEM electrolysis. IOP Conference Series: Earth and Environmental Science, 371, p.042022. doi:https://doi.org/10.1088/1755-1315/371/4/042022.